Coca-Cola boosts safety, traceability and efficiency with ID card
11 million drinks, 90,000 customers, 21 brands : in Belgium as elsewhere, everyday life without Coca-Cola is unthinkable. At the Coca-Cola European Partners Belgium plant in Wilrijk, five production lines produce some 4,000 pallets of soft drinks a day. To make certain everything runs safely and smoothly, the machines were recently fitted with a centrally managed RFID access control system from Siemens.
“The site in Wilrijk came about as a merger of 3 plants,” says Electrical & Automation Engineer Dirk Lembrechts, who has worked at Coca-Cola for 28 years. “Here we mainly produce PET bottles ranging in size from 0.25 to 2 liters for the Belgian market. Besides this, there is also one production line that is used for the iconic glass Coca-Cola bottles.”
All production machines at Coca-Cola European Partners Belgium are fitted with access control, ensuring that only authorized persons can operate the machines or change specific parameters. “Until recently we used a system featuring a variety of drop-shaped RFID tags,” says Dirk. “Each tag had a different color and granted different access rights and authorisations.” But that system had a number of drawbacks.
Flexible access rights 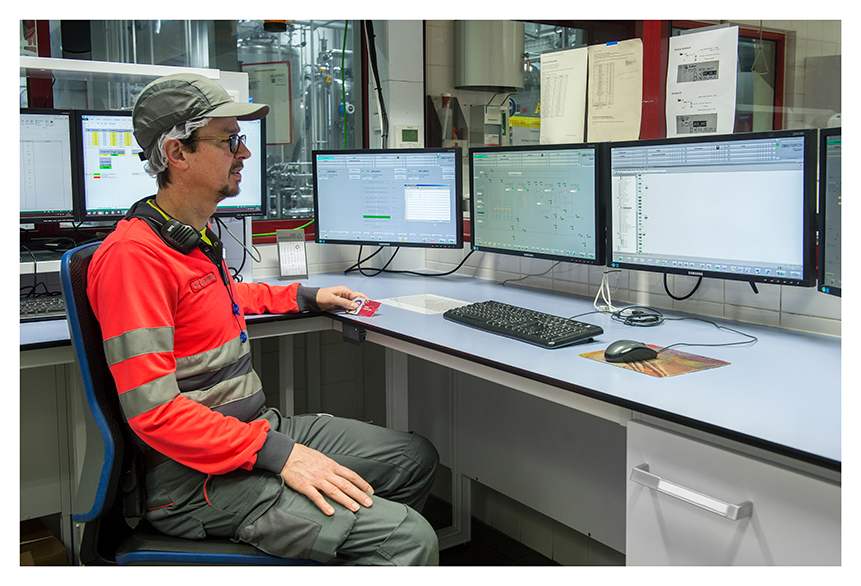
Dirk’s team turned to preferred supplier Breemes to imple¬ment a new access control system. As a regular electrical engineering partner of Coca-Cola European Partners
Belgium, this local integrator had already also provided the industrial automation in Wilrijk.
“The new solution had to be better than the old one in all respects: user-friendliness, flexibility and safety,” says Joren Marteaux, technical commercial representative at Breemes. “What’s more, it had to integrate seamlessly with the current industrial automation. Because Coca-Cola European Partners Belgium runs on SIMATICS PCS 7, we quickly got in touch with Siemens. Their SIMATIC RF1000 solution met all our expectations.”
“The new solution had to be better than the old one in all respects”
First of all SIMATIC RF1000 eliminates the tags: employees simply use their existing ID card, which reduces the risk of loss and misuse and cuts costs. Lost ID cards can be deactivated immediately. What’s more, the system runs on a central database, and access and management rights can be assigned at individual level. At the same time it is now much easier to assign access rights to new colleagues.
Safety and traceability
But there’s more. Besides access rights, SIMATIC RF1000 also offers a high level of traceability in the form of the ‘Audit Trail’. “A record is kept of every login to a machine,” explains Dirk. “That lets us see who changed particular parameters, so if there is a problem we can resolve it quickly and get production back on track.
“Colleagues are a lot more aware of their individual responsibility. Few interventions are necessary”
Bear in mind that the aim isn’t to admonish people, but to troubleshoot problems as quickly as possible and get production back on track.”
One effect of the Audit Trail is a reduction in the number of incidents. Dirk: “We’ve been using the system for two years now. In that time we’ve noticed that colleagues are a lot more aware of their individual responsibility. Which in turn means that few interventions are necessary.”
Ease of use
The operators themselves are the ones to talk to about how easy the SIMATIC RF1000 system is to use. “It’s now much simpler to log in”, says Dirk. “The RFID reader is incorporated into the machines’ Comfort Panel.
Someone working at the machine can just leave their cardin it the whole of that time. In the control rooms the systemcan even be installed under the desk, in which case all you need do is to place your ID card on top of the desk to log in and start working.”
SIMATIC RF1000 has now been integrated into most machines in Wilrijk, including palletizers, wrappers and handle applicators. And Syrup Room operation – the heart of production – has been linked up to the system. Dirk: “We have around 60 active licenses, split between engineers and operators. They all agree that this system is a huge leap forward when it comes to safety, reliability and ease of use.”
Engineering Support
itsme Breemes Industrial Automation knows your world. That’s what we say, but we’d much rather show you in practice. We get to work for you as soon as we visit you. And how that works is shown, among other things, by our engineering support. See this service as the sounding board for your automation. You will receive feedback on a concept, get insight in your processes and discover where and how to achieve greater efficiency. And for a solution we start from best practices and from our product knowledge. For that is what you can expect from us: no coloured story about one single brand, but independent customized advice for the improvement of your processes. This is how we help you to increase your profits, reduce your risks and decrease your costs.
Are you looking for a review of your design? Is there a new machine in your production hall and do you want to make sure that it is properly connected? We are there from the introduction, definition and design, to the preparations, implementation and follow-up.
Make the right choices with us for your automation project and contact us for a first acquaintance.