IMA updates its machines with technical support from itsme ELEKTRES
The ability to adapt to change is key for a business’s competitiveness and, for those based on technology, it is essential to have good technical advice in order to move forward. itsme ELEKTRES is the ideal partner in such cases. As well as its first-hand experience with top brands and manufacturers, it also offers a full technical support service, from the analysis of the client’s needs to implementation of equipment, as well as any changes that may be needed in the future.
IMA’s journey
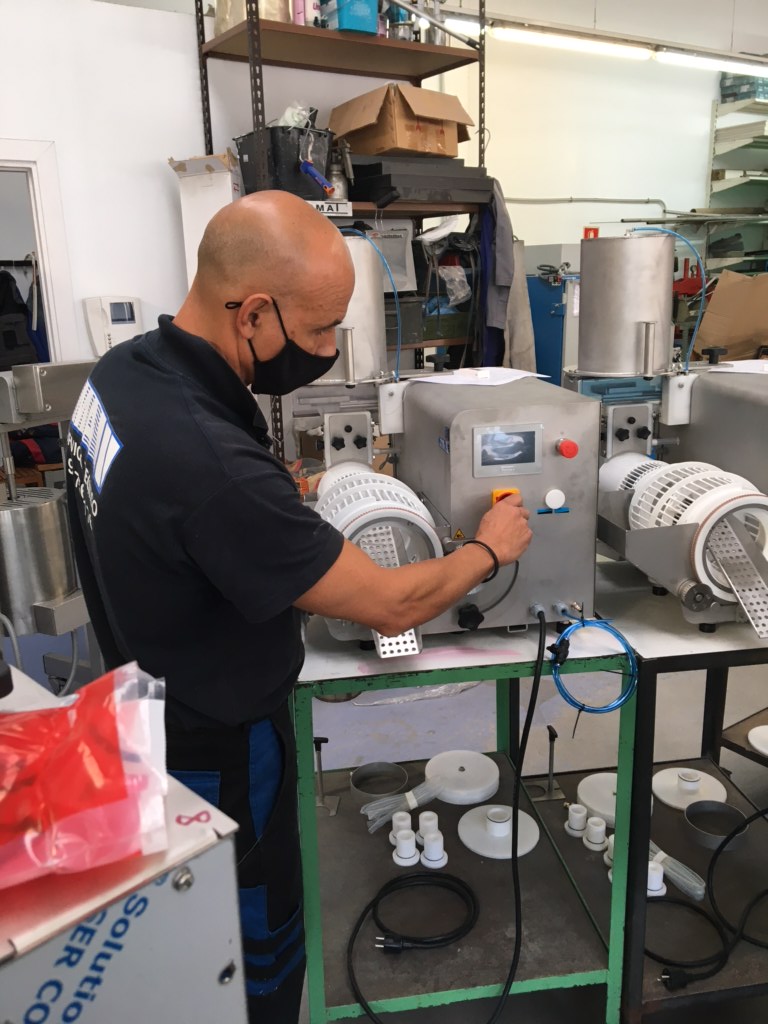
IMA is a family business with more than 30 years’ experience in automatic machinery for the food sector. In the early days, it focused on machines that cut cold meats, and later it became the first company to introduce vacuum packaging into Spain. Over the years, it came to specialise in providing machinery for butchers. Once these butchers started making their own products, IMA discovered a new niche in an automatic machine for making croquettes. That was almost 20 years ago; since then it has specialised in manufacturing croquettes and meatballs, which are now mainly used in the hospitality and catering industry. IMA’s story shows its clear future vision and know-how in adapting to the ever-changing needs of its clients, providing solutions that support their operations and which even open up new business opportunities. Most recently, it teamed up with itsme ELEKTRES to put a system in place that enables any adjustment to be carried out in a simple and efficient way.
itsme ELEKTRES recommended custom-built electronics and Schneider’s SoMachine platform
Initial analysis showed that the machine was controlled through non-reprogrammable electronic cards. It was a custom-made solution carried out by a manufacturer of non-standard electronics that was inflexible when it came to making changes. In other words, any small adjustment could mean having to redesign the whole program from scratch, making it very limited and preventing improvements or new functionalities from being brought in. Because of this, itsme ELEKTRES suggested using a standard solution that consisted of a PLC [Programmable Logic Controller] by Schneider, a leading manufacturer that guarantees security in terms of quality and supply chain response. The second step was developing the application. itsme ELEKTRES designed a custom-made application, which simplifies the programming of equipment.
“Everything is much easier with this system”, says Jorge Argona, IMA’s technical director. “Now, when we’re asked to make any changes or increase its functionalities, we contact the itsme ELEKTRES technical team, transfer the request to them and they take care of the reprogramming”, Jorge explains. The clients themselves can also make changes to their machines, since the program comes on an SD card. This makes them flexible and self-sufficient when it comes to making changes.
“Everything is much easier with this system”
The new system also enables different machines to connect. This is very useful, bearing in mind that it is a small machine, but with a large production quantity. For example, the machine has a container that can hold 8 kg of product, but some clients produce large quantities and need bigger containers. With the current software, they can easily connect to external stuffing machines that have a capacity of up to 1,000 kg. Before, it was complicated and almost unfeasible to interconnect machines in this way, since it meant using a very outdated procedure (changing the electrical control panel and other components), which took a lot of time and effort.
New selling points
At the same time, itsme ELEKTRES also recommended replacing the control panel with a touch panel in order to improve usability, since up till then the machines had an electronic screen with very few functions. The new graphic interface is highly intuitive and contains a fully functioning menu that allows the parameters, such as cutting speed, to be changed easily. It also provides the client with basic feedback on operational data, such as the amount of product it has made. “All these improvements are selling points for us”, says Jorge. He adds that they have heard from clients who already have the machine and now want to adapt it, especially when they see the new digital screen, the menus and its speed and versatility. IMA has offered them a renewal plan so they can access the new system.
“All these improvements are selling points for us”
When it comes to sales, itsme ELEKTRES’ involvement also gave IMA a major competitive advantage with its kneading machines, another product in its portfolio. These machines have a container with temperature control. Conversion to the same system meant that the cooking temperature is now better regulated. This helps the desired temperature to be reached faster and maintained much more accurately. “Our clients really value this accuracy, as it significantly improves the cooking process”, says Jorge.
“There are lots of suppliers, but we’re staying with itsme ELEKTRES”
Moreover, IMA says that “the relationship with itsme ELEKTRES couldn’t be better”. “It hasn’t been easy, because the level of change that we asked for meant many hours’ work, which we appreciate”, says Jorge, adding: “when there’s been a version change or we’ve needed anything, they have always been at our disposal”. “There are lots of suppliers and a lot of competition, but we’re staying with itsme ELEKTRES because we’re very happy with them”, Jorge concludes.
The 179 sets of machines that itsme ELEKTRES supplied the business with in 2019 is proof of IMA’s satisfaction.
IMA also provides technical support
IMA is located in Barcelona where they have been manufacturing a range of food processing machines for the industry for over 30 years. Think of machines in different sizes, with automatic egg and breadcrumb dispensers and filling machines to produce meatballs and croquettes. Their portfolio also includes hot kneading machines to prepare all sorts of food mixtures and sauces, all for the professional industry, such as caterers and hotels. Additionally, IMA also provides their customers with technical support on their machinery. They also give advice on various techniques and systems related to the development of their customers’ products.