Met teamwork en technologie naar Industrie 4.0
Trillingssensoren verbeteren de betrouwbaarheid in de levensmiddelen industrie
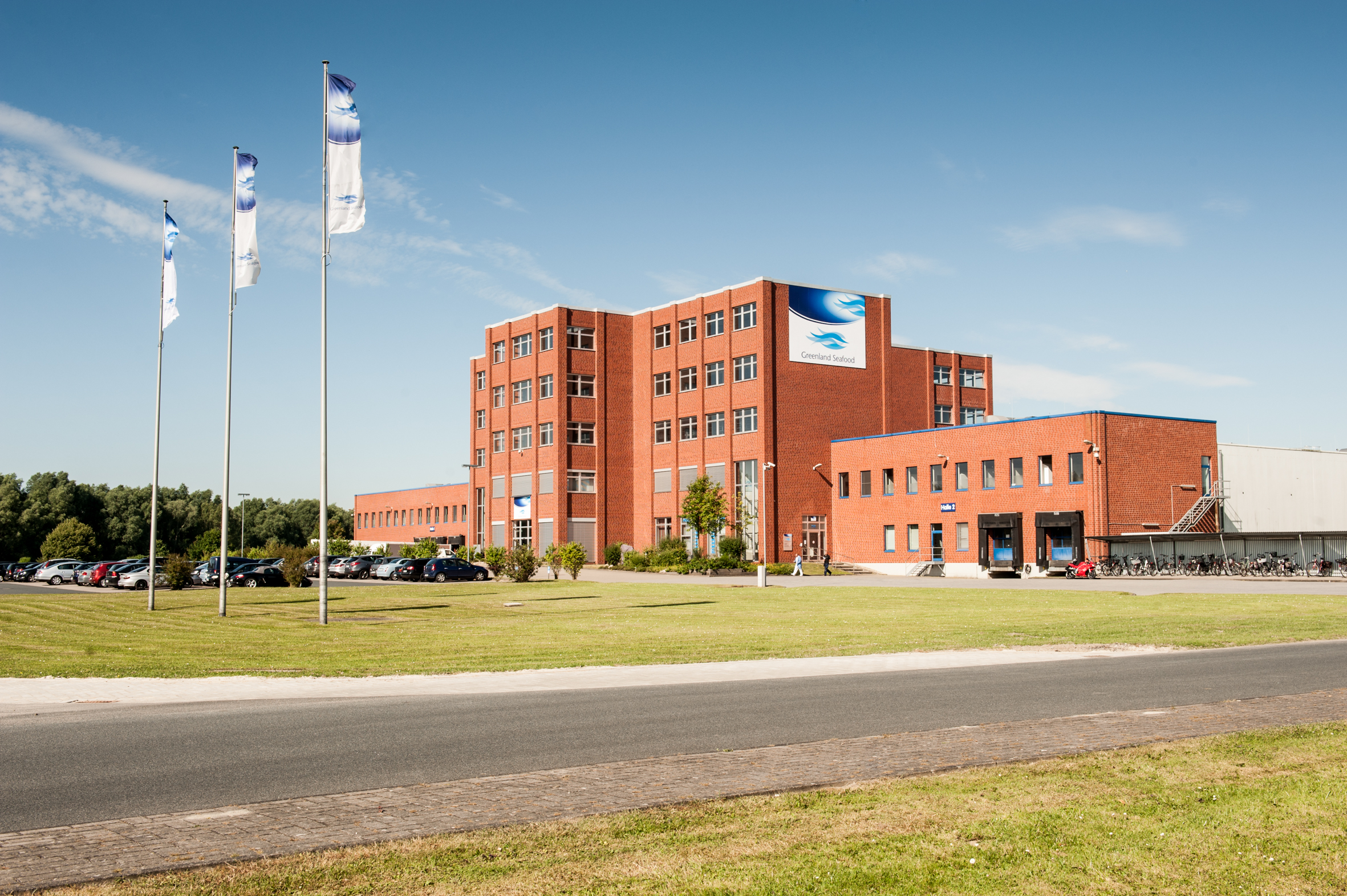
Sneller, hoger, verder – voor veel investeringen zijn er overtuigende argumenten en een return on investment kan gewoonlijk worden berekend met een paar muisklikken. Het is echter moeilijker om de noodzaak van een aankoop te bewijzen als een gebeurtenis misschien niet eens plaats vindt. Levensmiddelenproducent Greenland Seafood heeft besloten om te investeren in zijn apparatuur en heeft een systeem geïnstalleerd om belangrijke motoren te bewaken.
Industrie 4.0 betekent hoge normen in industriële productie: het introduceren van digitale concepten om systemen te verbeteren en flexibeler te maken, gedreven door kostenbesparing op de eenheidsprijzen en het vermogen om flexibel te reageren op eisen van de markt. Vergeleken bij Batch Size 1 en zelforganiserende productie lijkt de dagelijkse bedrijfsvoering eerder doorsnee. Maar het is beslist de moeite waard in de richting van Industrie 4.0 te denken. Heel vaak zijn het de schijnbaar onbelangrijke verbeteringen die gebruik maken van moderne automatiseringstechnologie, die de gebruiker de voordelen bieden van digitalisering zonder een hoog prijskaartje. Zoals bij Greenland Seafood.
Productie aan de kust
Greenland Seafood haalt zijn basismateriaal uit visgronden van over de hele wereld. Als een van de grootste producenten van vissticks, gebakken vis, en naturel filet, maken ze 1,3 miljoen vismaaltijden per dag in Wilhelmshafen, niet ver van de Jade-Weser-Port. Maar om de eindklant te laten kiezen tussen Greenland Seafood’s gepaneerde klassiekers, snacks en visspecialiteiten, moeten de systemen op de achtergrond de hele dag draaien. Productietechnici zien het koelsysteem als het technische hart van de installatie. Het ligt strategisch in het midden van de fabriek en verdeelt de koeling over de verschillende delen van de fabriek, van productie, verpakking en opslag tot airconditioning. Als dit systeem defect raakt, dan komt de hele productie tot stilstand.
“Mijn ervaringen met statusbewaking en Industrie 4.0 zijn: iedereen wil het, maar niemand weet wat het is”
Neem de productie van vissticks als voorbeeld: honderden vissticks worden gezaagd uit 7,5 kilo bevroren blokken vis en dan gepaneerd. Na onderdompeling in een friteuse met olie van 185 °C, worden de stukken vis verplaatst naar een van de zeven spiraalvriezers om ze klaar te maken voor verpakking en vervoer, op temperaturen van -30 °C en lager. “We kunnen simpelweg niet produceren zonder deze koude temperaturen”, zegt plant automation engineer Joachim Gerken, als hij het uitvalscenario van een stilgevallen fabriek uitlegt. “Er werken hier vierhonderd mensen. Bovenop de loonkosten zijn er dan ook nog andere verliezen – machinekosten, vernietigd basismateriaal en de kosten van stilstand voor onze klanten.” Het kost bij elkaar al snel meer dan € 10.000 per uur als zo’n belangrijk gedeelte als het koelsysteem zou uitvallen.
Voorspellend onderhoud
De interesse van Joachim in voorspellend onderhoud nam toe als gevolg van een eerder incident. "Net toen volgens ons onderhoudsschema aan een hogedrukcompressor onderhoud werd gepleegd, raakte een andere defect met schade aan een lager. Die stond voor een volgende keer op het onderhoudsschema. Ofschoon de overblijvende koelgeneratoren in staat waren om de storing te compenseren, benadrukte dit incident dat we actie moesten ondernemen bovenop onze reguliere, halfjaarlijkse, controles”, zegt Joachim.
Het is aan Martin Zielinski te danken dat uit deze nood een klein project ontstond. Hij is accountmanager bij itsme Schultz+Erbse en draagt regelmatig suggesties en ideeën aan om de fabrieksprocessen van zijn klanten te optimaliseren. “Ik bezoek ook regelmatig de verschillende technische ruimtes bij Greenland Seafood en praat daar met de operators over mogelijkheden om te verbeteren”, zegt Martin. Dus toen hij hoorde over een relatief nieuwe sensor die door Turck wordt gemaakt, waarmee de status van de motor dag en nacht kan worden bewaakt, riep hij de mensen in de fabriek bij elkaar. Martin legt de situatie uit: “Joachim stelde een testsessie voor om de nieuwe sensoren uit te proberen, die door Phil Whorton van automatiseringsspecialist Turck samen met ons werd uitgevoerd.”
“We zien de voordelen van langetermijnmetingen nu al: verbeterde betrouwbaarheid en nauwkeuriger kunnen bepalen welk apparaat onderhoud nodig heeft en wanneer”
“We hebben de trillingsensor al twee jaar in ons productenpakket”, bevestigt applicatie-ingenieur Phil. “Mijn ervaringen met statusbewaking en Industrie 4.0 zijn: iedereen wil het, maar niemand weet wat het is. Met deze sensor bewaken we alle draaiende of bewegende machines, motoren, ventilatoren, tandwielen en pompen, zodat we conclusies kunnen trekken uit hun status.” De sensor bepaalt zowel de snelheid als de acceleratie van de X- en Z-assen en meet de temperatuur. Aan al deze data en in het bijzonder aan veranderingen die mogelijk optreden, wordt de huidige status ontleend. De mate van trilling betekent dat conclusies kunnen worden getrokken over de toestand van de lagers, terwijl de snelheid helpt bij het controleren van de ophanging en van elke onbalans in de motor.
Uitgangspunten die voldoende waren om tot een beslissing voor een testsessie te komen. Het Greenland Seafood team besloot al snel dat de twee HD4- en HD5-hogedrukcompressors geschikte kandidaten waren. De HD5 had al nieuwe slijtvaste onderdelen, omdat hij net een onderhoudsbeurt had ondergaan. HD4 was een van de motoren op de lijst die wat meer slijtage had moeten laten zien. Nu moesten alleen de sensoren nog gemonteerd worden, waarbij Joachim voor de magnetische versie koos. Daarna moesten ze van draad worden voorzien en aan een robuuste IP67 PLC van Turck verbonden worden, die zonder schakelkast was gemonteerd en die de data zou evalueren en visualiseren.
Constante waarden voor een betere beslissing
Het voordeel waar ze op hoopten, werd snel bevestigd. “Als je de vroegere trillingsmetingen vergelijkt met de nieuwe constante waarden, dan stemmen die goed overeen. Waar we voorheen tweemaal per jaar informatie over de status van een motor ontvingen via een externe dienstverlener, gebeurt dit nu de hele dag door – inclusief meldingen via SMS en e-mail”, zegt Joachim. “We kunnen de voordelen van langetermijnmetingen nu al zien: het verbetert onze betrouwbaarheid en we kunnen veel nauwkeuriger bepalen welk apparaat onderhoud nodig heeft en wanneer. Niet alleen volgens een onderhoudsschema, maar gebaseerd op de actuele toestand van het apparaat“, vult hij aan.
De test is nog niet helemaal afgesloten: de halfjaarlijkse metingen door de dienstverlener worden nog tot nader order uitgevoerd en dienen als controlemetingen. Het gaat hierbij niet in eerste instantie om het besparen van geld, maar vooral om meer betrouwbaarheid in de productie, benadrukt Joachim. “Dat was ook de mening van ons management. Deze investering geeft ons op korte termijn immers geen winststijging.” Vanwege de coronacrisis is het uitrusten van de andere hogedrukcompressors uitgesteld maar zeker niet geannuleerd. “Binnen een jaar gaan we ook de andere motoren met deze sensoren bewaken en de nieuwe ervaringen gebruiken om te beslissen welke motoren in de fabriek we vervolgens hiermee gaan uitrusten“, zegt Joachim Gerken met een vooruitblik op de toekomst.